3 Simple Techniques For Welding Inspection
Table of ContentsMore About Welding InspectionWelding Inspection - TruthsAll About Welding InspectionTop Guidelines Of Welding Inspection4 Simple Techniques For Welding InspectionExcitement About Welding InspectionThe 5-Minute Rule for Welding Inspection
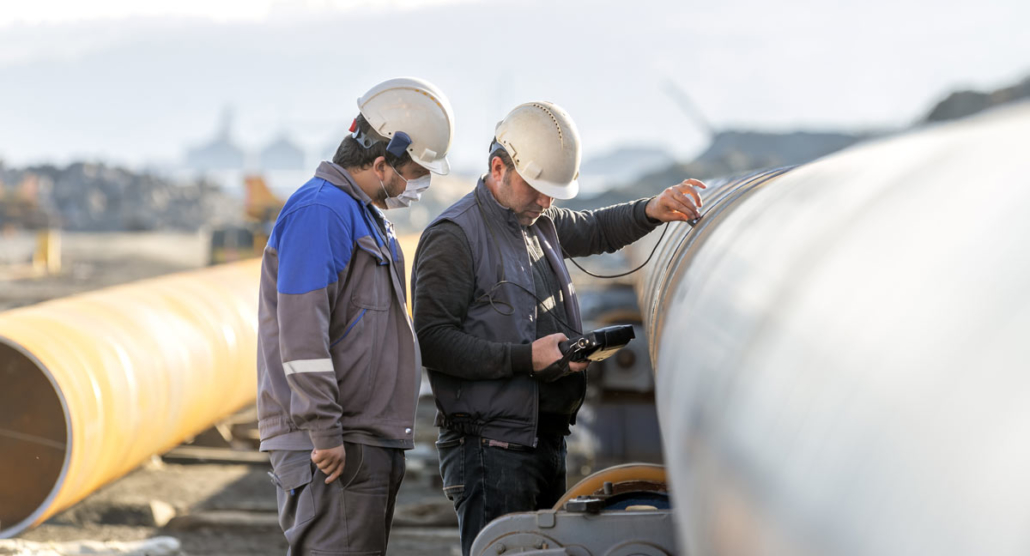
2 Senior Welding Examiner levels with expertise including ferrous and also nonferrous products. Our approach to weld evaluation and monitoring It is vital to discover any issues with welds prior to they escalate or right after they occur so they can be fixed as rapidly as possible. Aspect's weld assessors examine the top quality of welds at every step of the fabrication process previously, throughout, and also after welding.
Customers have varied from personal to public and also huge to small; the focus is constantly on keeping a high standard as well as compliance with the appropriate code to make certain that your job has actually met all of the necessary requirements be they code, local, industrial or governmentally enforced regulations as well as or needs.
Unknown Facts About Welding Inspection
Swirl present screening, In eddy current screening, electromagnetic currents create a magnetic field that connects with the subject, generating localised swirl currents. Changes in phase as well as magnitude indicate issues and also can be measured to quantify dimension, shape and place. High regularities are used to gauge problems at or near the surface, while reduced frequencies can penetrate deeper within the test subject.

Different features of the weld may be evaluated throughout a welding analysis, some regarding the weld dimensions as well as others about using stoppages of the weld. The dimension a weld might take is critical since it can directly associate to the weld's sturdiness and also associated performance, small welds may not stand up versus pressures used while in solution.
Excitement About Welding Inspection
These are blemishes with or close with the weld, that can or not connect to their measurement and/or location, obstruct a weld from conference its made performance. Generally, such gaps, when are of unwanted dimension or place, are called welding issues as well as can also sometimes trigger early weld falling short though the reducing of the weld's resilience or though creating anxiety levels within the component of the weld. Welding Inspection.
The most standard purpose is to determine if the weld has a suitable as well as leading quality for the made program. To be able to access a weld's top-notch, there must be some benchmark to which its functions can be compared to. It is inaccurate to try and access a weld's quality in the absence of some particular authorization demands.
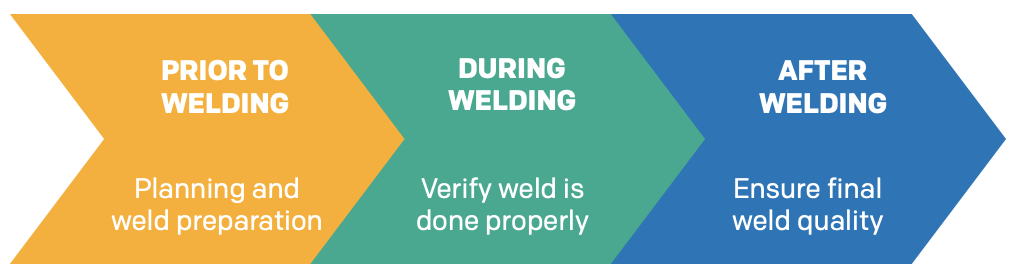
Welding Inspection - An Overview
This method is carried out in a workshop or field while the welding is being done. The important things that are visually checked include the welder's certification, slag elimination, joint preparation, climate condition, current used, as well as problem of the electrode. 2- Magnetic Fragment Testing This test is utilized to discover any kind of surface area or hardly subsurface defects in a weld.
Bits of iron are after that related to the magnetic field as well as if there are any type of defects, the particles of iron will certainly develop around the issue, which shows where the flaw is as well as why it occurred. 3 Liquid-Penetrant Evaluating This test will certainly identify defects in the surface of the weld like porosity as well as hairline fractures.
A designer is then applied that will show if any kind of defects show up. 4 Ultrasonic Examining This test is achieved by the use audio vibrations, which are then sent through the bonded joint. The signals obtained on a glass display will certainly establish if there are any kind of flaws in the joint of the weld.
More About Welding Inspection
5 Swirl Current Testing This test will certainly show extremely tiny fractures and is completed by the use a circular coil that lugs alternating currents, which is positioned near the weld. The alternating currents will develop an electromagnetic field, which will connect with the weld as well as consequently, create an eddy present.
The resulting indentation dimension is referred to as a firmness gauging table. 8 Damaging Examining This test is a devastating test that is achieved by reducing the completed weld into items, this is per the code for origin bend, face bend, tensile test, as well as side bend. It is made use of to locate slag addition, porosity, and also undercutting flaws in read here welds as well as is really efficient.
This approach is performed in a workshop or area while the welding is being done. Things that are visually inspected consist of blog the welder's certification, slag removal, joint preparation, weather, current used, as well as problem of the electrode. 2- Magnetic Fragment Testing This test is utilized to discover any kind of surface or barely subsurface issues in a weld.
Not known Details About Welding Inspection
Particles of iron are then put on the electromagnetic field and also if there are any kind of issues, the fragments of iron will certainly accumulate around the flaw, which shows where the problem is and why it occurred. 3 Liquid-Penetrant Evaluating This test will discover flaws in the surface area of the weld like porosity and hairline cracks.
A programmer is after that applied that will show if any type of flaws are noticeable. 4 Ultrasonic Testing This test is accomplished by the use sound vibrations, which are then transmitted via the bonded joint. The signals obtained on a glass display will certainly identify if there are any type of flaws in the joint of the weld.
5 Swirl Current Screening This test will show very little fractures as well as is completed by the use of a round coil that carries alternating currents, which is positioned near the weld. The rotating currents will certainly develop a magnetic area, which will connect with the weld as well as in turn, create an eddy current.
The Definitive Guide for Welding Inspection
The resulting imprint dimension is referred to as a firmness gauging table. 8 Damaging Checking This examination is a damaging examination that is completed by cutting the completed Click This Link weld right into items, this is per the code for origin bend, face bend, tensile test, as well as side bend. It is utilized to situate slag inclusion, porosity, as well as damaging issues in welds and is extremely efficient.